Digitalisierung: Modernisierung von Gießereien mit wenig Aufwand
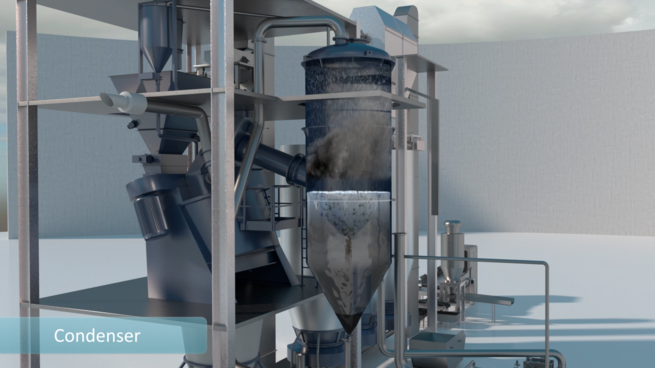
Die Gießereiindustrie ist eine traditionsreiche Branche und trotz vieler Wandel nicht aus der Wirtschaft wegzudenken. Um mit dem branchenübergreifenden Ziel einer digitalisierten Produktion Schritt halten zu können, müssen Gießereien nachrüsten. Eirich zeigt, dass oft schon kleine Nachrüstungen und Modernisierungsmaßnahmen ausreichend sind, um veraltete Bestandsanlagen auf einen neuen Stand zu bringen und die Effizienz zu steigern.
Hardheim, 24. Juni 2024: Die Gießereiindustrie darf sich bei der Digitalisierungswelle in anderen Branchen nicht abhängen lassen. Ein Schlüssel zur Zukunftssicherung liegt in der Modernisierung bestehender Anlagen. Viele Maschinen aus den 1980-90er und 2000er Jahren funktionieren noch einwandfrei, aber ihre Steuerungssysteme sind technologisch veraltet. Nicht immer sind Neuanlagen oder hohe Investitionen erforderlich; oft genügen schon Nachrüstungen und kleinere Modernisierungsmaßnahmen, um auf dem neuesten Stand zu sein. Vor allem die Steigerung der Energieeffizienz ist hier ein Hauptanliegen, um die Gießereien wirtschaftlicher aufzustellen. Ein geringer Co2-Fußabdruck wird immer wichtiger und Klimaneutralität ist auch in Gießereien längst kein Wunschtraum mehr, sondern in naher Zukunft ein Muss.
Eine Optimierung an gezielter Stelle von Bestandsanlagen kann eine kostengünstige Lösung bieten. Eirich setzt bei den Steuerungskonzepten an – ein wichtiger Hebel, um die Gießereien wirtschaftlicher aufzustellen.
Up to date durch Steuerungsumbau
Der erste Schritt einer Modernisierung liegt in der Bestandsaufnahme für den sinnvollen Einsatz neuer Sensorik. Eine innovative Steuerlogik für die Sandaufbereitung bietet großes Potenzial.
Durch eine intelligente Sandregelung unter Berücksichtigung einer Tagesmodell-Auftragsbetrachtung werden vorausschauend Neusand- und Additiv bedarfsgerecht errechnet. Das Inline-Prüfgerät QualiMaster AT1 liefert mit drei Messungen pro Charge innerhalb von 40 Sekunden die Werte von Verdichtbarkeit und Scherfestigkeit, welche über die Software „Sandreport“ erfasst und analysiert werden. Über die relevanten Chargendaten aus dem aufbereiteten Formstoff und dem Feuchtekorrektur-Tool AC1 wird das Sandsystem entsprechend den Vorgaben gesteuert und gegebenenfalls korrigiert. Die intelligente Sandregelung erfolgt über die Software „SandExpert“ mit einer vorausschauenden Neusand- und Additiv-Bedarf-Berechnung. So steht der Formanlage der passende Formstoff jederzeit für das jeweilige Guss-Produkt zur Verfügung. Der Altsand wird mit genau so viel Bentonit, Neusand und Additiven aufgefrischt, wie dieser beim folgenden Gießprozess verliert.
Das schont Ressourcen und spart Zeit. Der Gießer kann so auf ein effektives Rohstoffmanagement mit maximaler Flexibilität in der Produktionsplanung sowie stabile Prozesse und reproduzierbare Ergebnisse zurückgreifen.
Einsatz von KI-Tools
Die digitale Darstellung der Produktion ist ein wichtiger Schritt für die Zukunftsfähigkeit der Branche. Künstliche Intelligenz dient in vielen Fällen zur Qualitätsverbesserung des Produkts und somit der Senkung der Ausschussrate.
„Es gibt immer noch unbegründete Berührungsängste bei dem Thema Digitalisierung. KI wird in erster Linie zur Unterstützung der Fachkräfte eingesetzt. Die Stärke dieser Tools liegt darin, eine große Menge gesammelter Daten in einem bestimmten Kontext zu interpretieren und so fundierte Entscheidungsgrundlagen zu liefern. Durch ständiges Lernen kann eine nahezu hundertprozentige Genauigkeit bei der Prognose produktionstechnischer Parameter erreicht werden“, erläutert Salesmanagerin Maria-Luise Liepe.
Mit einer kombinierten Datenanalyse aus Formstoffaufbereitung und Formanlage sowie intelligenter Sensorik und der Datenanalyse-Software „LogLizer“ können Systemgrenzen überwunden werden. Der Gießprozess kann so auf mehreren Ebenen betrachtet, analysiert und gesteuert werden. Die Abfrage der Daten ist jederzeit und überall auf PC, Tablet und Smartphone möglich.